Every business owner, from the corner bakery to a multinational corporation, knows that labor costs are a significant part of their expenses. But have you ever stopped to think about how those costs are classified? Beyond the simple breakdown of wages and salaries, there’s actually a deeper categorization that can significantly impact a business’s financial planning and decision-making. This is especially relevant today, with rising minimum wage laws, automation advancements, and the changing nature of work. In this article, we’ll dive into the two main classifications of labor costs and explore the implications for businesses and workers alike.
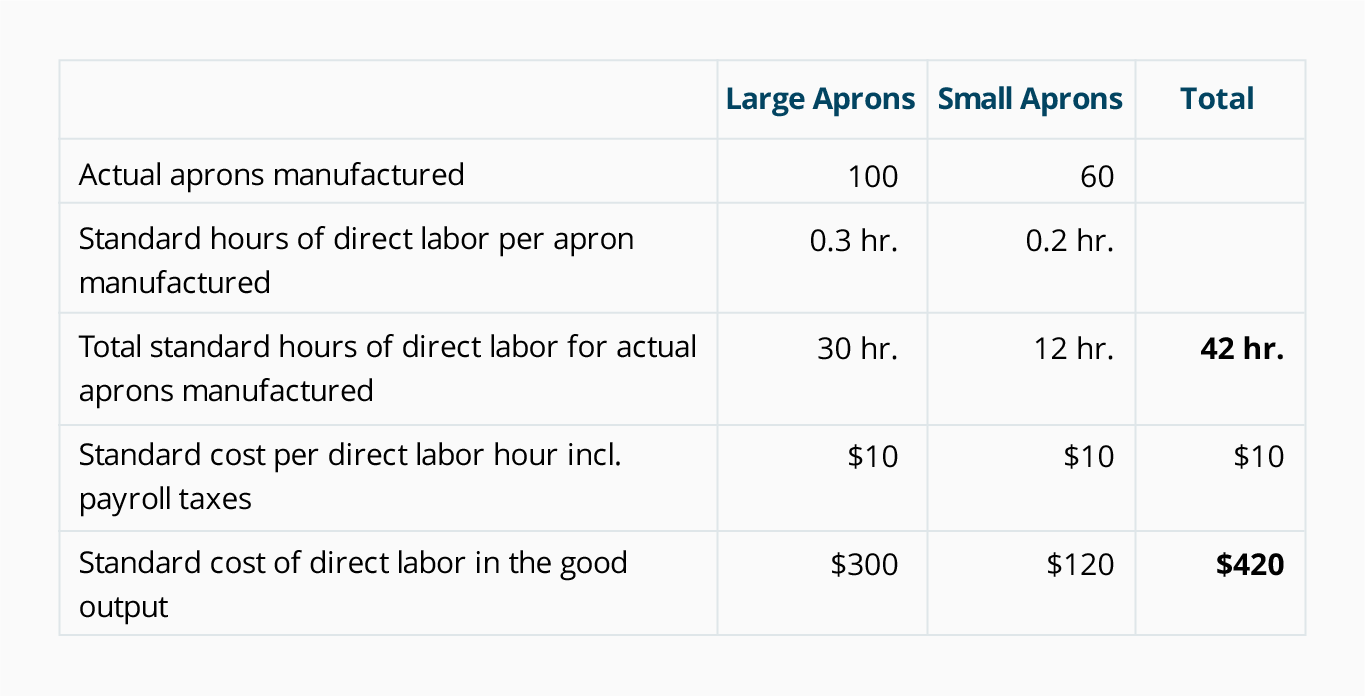
Image: sheldonqoespinoza.blogspot.com
I remember starting my own small business and being overwhelmed by all the different costs I had to track. While I easily understood the cost of raw materials and utilities, I wasn’t sure how to categorize labor costs, which seemed to fluctuate every month. It wasn’t until I spoke with an experienced accountant that I realized there were two distinct categories, each impacting my business differently. This revelation helped me gain a clearer picture of how to manage expenses and make informed decisions about my workforce.
Direct vs. Indirect Labor Costs: The Foundation of Financial Understanding
Understanding the distinction between direct and indirect labor costs is crucial for businesses to accurately determine the cost of producing goods or services and therefore set prices that guarantee profitability. This distinction is especially important for manufacturing and service industries that rely heavily on human resources to create their offerings.
Direct labor costs, as the name suggests, are directly tied to the creation of a product or service. They represent the wages and salaries paid to employees who are actively involved in the production process. For example, in a car factory, the workers assembling the vehicles, the mechanics performing maintenance, and the welders responsible for the car’s framework all represent direct labor costs. Similarly, a restaurant’s chefs, waiters, and dishwashers contribute directly to the service provided to customers and are therefore classified as direct labor.
Direct Labor Costs: A Closer Look
Here are some key characteristics of direct labor costs:
- Directly traceable to output: Every hour spent assembling a car, cooking a meal, or writing a piece of code can be directly linked to the final product.
- Variable costs: Direct labor costs change depending on the volume of production. If a car factory produces more cars, it will need more workers, leading to increased direct labor costs.
- Essential for production: Without direct labor, there would be no output. It’s the cornerstone of the production process.
Indirect Labor Costs: The Support System
In contrast to direct labor, indirect labor costs are those incurred by employees who are not directly involved in the production process but are essential to supporting it. These costs represent the salaries and wages of employees who ensure that the direct labor force has the resources and environment to function efficiently.
Think of it like a football team. While the players on the field are crucial for scoring touchdowns, the coaches, trainers, and support staff are essential for their success. The coaches strategize, the trainers keep them healthy, and the support staff manage logistics and equipment. Similarly, in a business, indirect labor costs cover employees who provide essential support, such as:
- Supervisors: Overseeing the work of direct labor and ensuring quality control.
- Maintenance staff: Keeping the machinery and equipment in working order.
- Human resources: Hiring, training, and managing employees.
- Accounting and finance: Tracking expenses, managing payroll, and ensuring financial stability.
- Marketing and sales: Promoting the products or services and securing customers.
Image: www.coursehero.com
Understanding the Impact of Labor Costs
Both direct and indirect labor costs are crucial to a business’s success. Direct labor costs are directly tied to revenue generation, while indirect labor costs ensure the smooth operation of the business and create the environment for direct labor to thrive. Recognizing the importance of both categories is essential for:
- Cost accounting: Accurately calculating the cost of goods sold and determining the profitability of different products or services.
- Pricing strategy: Setting prices that cover both direct and indirect labor costs and ensure a healthy profit margin.
- Operational efficiency: Identifying areas where indirect labor costs can be optimized to reduce unnecessary expenses.
- Human resources management: Effectively managing employee salaries and benefits within both direct and indirect labor classifications.
Trends and Developments in Labor Costs
The world of work is constantly evolving, bringing with it new challenges and opportunities for businesses. Here are some key trends and developments that are shaping how we think about labor costs:
- Rise of automation: As artificial intelligence and robotic technologies advance, we’re seeing a gradual shift from human-intensive to automated labor. This has the potential to both reduce direct labor costs and create new job opportunities in the development and maintenance of these technologies.
- Remote work: The rise of remote work has changed the landscape of labor costs. Businesses can now access a wider talent pool, potentially leading to more competitive salaries and the need to address potential challenges related to managing remote teams.
- Gig economy: The increasing popularity of platforms like Uber and Upwork has led to the growth of the gig economy, where individuals work on short-term projects and contracts. This can result in more flexibility for workers but also creates uncertainty in their earnings and benefits.
- Minimum wage laws: The increasing minimum wage laws across various jurisdictions can significantly impact direct labor costs, particularly for businesses with large numbers of low-wage workers. This can lead to strategies like automation and price increases.
Tips and Expert Advice: Managing Labor Costs Effectively
Given the dynamic nature of labor costs, businesses need to be proactive in managing them. Here are some tips and expert advice to ensure financial stability:
For direct labor costs:
- Improve efficiency: Encourage cross-training and streamline production processes to optimize productivity and reduce labor hours required for each unit of output.
- Negotiate wages: Be transparent about your needs and work with employees to find solutions that balance competitive wages with financial sustainability.
- Use technology: Explore automation and software solutions to reduce manual labor and optimize resource allocation.
For indirect labor costs:
- Outsourcing: Consider outsourcing tasks like accounting and human resources to specialized firms that can provide cost-effective solutions.
- Technology: Implement software that automates routine administrative tasks, freeing up time for more valuable activities.
- Review staffing levels: Ensure that your indirect labor force aligns with your operational needs and doesn’t unnecessarily inflate expenses.
Frequently Asked Questions about Labor Costs
Q: What are some of the common challenges associated with managing labor costs?
A: Some common challenges include:
- Fluctuating demand: Seasonal changes or unexpected shifts in market demand can create fluctuations in direct labor needs, leading to difficulties in managing wages and staffing levels.
- High turnover: Employees leaving the company can disrupt production flow and lead to increased recruitment and training costs, impacting both direct and indirect labor costs.
- Minimum wage increases: Mandatory minimum wage increases can significantly impact direct labor costs for businesses employing low-wage workers, potentially leading to price increases or reductions in staffing levels.
- Competition for talent: The demand for skilled labor in certain sectors can lead to increased competition for talent, driving up wages and making it challenging to attract and retain qualified employees.
Q: How can I accurately track labor costs and analyze their impact on my business?
A: Accurate tracking of labor costs involves:
- Time tracking systems: Implementing a system that accurately captures the time spent on specific tasks by direct labor employees helps determine the true cost of production.
- Budgeting and forecasting: Developing a budget that accurately estimates both direct and indirect labor costs based on projected production volumes and workforce needs.
- Regular analysis: Regularly reviewing labor costs against projections and identifying trends can help spot areas for improvement and adjustments.
- Financial software: Using financial software helps automate data collection, analysis, and reporting, making it easier to track labor costs and their impact on revenue and profitability.
Q: What are some strategies for reducing labor costs without compromising on quality or employee satisfaction?
A: Strategies for reducing labor costs include:
- Process optimization: Streamlining workflow, eliminating unnecessary steps, and implementing lean manufacturing principles can reduce labor hours required for production.
- Cross-training: Giving employees a broader skill set allows them to handle different tasks, promoting efficiency and reducing reliance on specialized personnel.
- Technology adoption: Investing in automation and software solutions can reduce manual labor in administrative tasks, production lines, or customer support, leading to cost savings without sacrificing quality.
- Employee engagement: Creating a positive work environment and offering opportunities for development can promote employee loyalty and reduce turnover, minimizing recruitment and training costs associated with high turnover rates.
Labor Costs Are Classified As Either
Conclusion
Understanding the distinction between direct and indirect labor costs is essential for businesses of all sizes. By accurately classifying these costs, businesses can gain a clearer picture of their financial performance, make informed decisions about pricing strategies, optimize resource allocation, and manage their workforce effectively. As technology continues to change the landscape of work, businesses need to be agile in adapting their approaches to managing labor costs and embracing new opportunities to benefit from both the cost-saving potential and the talent available in the evolving workforce.
Are you interested in learning more about specific strategies for managing labor costs in your industry? Let us know in the comments below!